The Intricate Art of Chinese Ceramic Creation
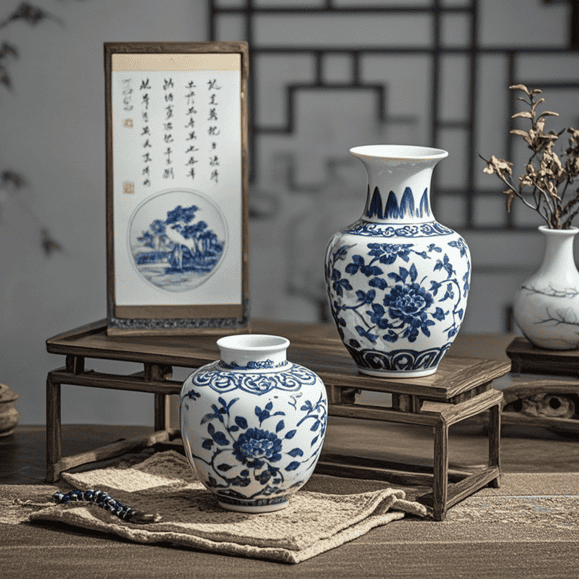
Chinese ceramics have a profound and illustrious history that spans millennia. The journey of crafting these remarkable artworks is an elaborate and time-honored process centered around the use of ceramic materials.
The initial step involves the careful selection of raw materials. For traditional Chinese ceramics, clay is the fundamental ingredient. Different types of clay, such as kaolin, are sourced based on their specific properties. Kaolin, renowned for its fine texture and ability to produce a pure white color when fired, is often a preferred choice. Additionally, other substances like feldspar may be incorporated. Feldspar serves multiple purposes; it helps in reducing the firing temperature required and contributes to enhancing the translucency and durability of the final ceramic piece.
Once the raw materials are gathered, they are meticulously blended in precise ratios. This mixture is then thoroughly kneaded, either manually by the skilled hands of an artisan or with the assistance of mechanical equipment. The objective is to achieve a homogeneous and pliable clay body. Subsequently, the shaping of the ceramic item commences. There are diverse techniques employed in this regard. Throwing on a potter’s wheel is a classic method where the artisan deftly manipulates the spinning wheel and the clay simultaneously to form symmetrical and aesthetically pleasing vessels. Another approach is molding, which utilizes plaster or other types of molds to produce multiple identical or intricately detailed pieces. During the shaping process, decorative elements can be added. Fine details can be carved into the surface by hand, or stamps and molds can be used to imprint patterns and designs, adding a touch of individuality and artistry to each ceramic creation.
After the shaping is complete, the ceramic piece must undergo a drying process. This is a critical stage as it requires slow and uniform drying to avoid cracking. The duration of drying can vary significantly depending on the size and thickness of the piece. It might take several days or even weeks. Once the drying is successfully accomplished, the first firing, known as the bisque firing, takes place. The bisque firing is carried out at a relatively moderate temperature, usually ranging from 900 to 1000 degrees Celsius. This firing serves to harden the clay, making it more structurally stable and porous, thereby preparing it for the subsequent glazing process.
The glazing stage is of utmost importance in the creation of Chinese ceramics. Glazes are concocted from a blend of minerals and oxides. These mixtures are carefully formulated to achieve a wide variety of effects. A simple clear glaze can be applied to accentuate the natural beauty and texture of the ceramic body, while colored glazes offer an extensive palette of possibilities. Colored glazes can create vivid and striking patterns, from delicate pastel hues to bold and vibrant colors. The application of the glaze can be done in several ways. Dipping the ceramic piece into a glaze bath ensures an even coating, brushing allows for more precise and detailed application, and spraying can be used for larger or more complex pieces.
Finally, the glazed ceramic piece is subjected to a second and final firing, known as the glaze firing. This firing occurs at a much higher temperature, typically between 1200 to 1400 degrees Celsius. The intense heat of the glaze firing causes the glaze to melt and fuse with the ceramic body. This fusion results in a durable and visually stunning finished product. The high temperature also imparts unique characteristics such as enhanced translucency and increased hardness to the ceramic.
The making of Chinese ceramics is a remarkable art form that demands years of apprenticeship and a profound comprehension of the materials and techniques involved. Each ceramic piece is a testament to the unwavering dedication and exceptional skills of the artisans who have faithfully preserved and advanced this ancient craft through the ages.